Description
Cooling Way: | Air Cooling |
---|---|
Control: | Manual |
Style: | Portable |
Frequency Range: | Intermediate Frequency |
Electric Current: | DC |
Type: | Continuous Seam Welder |
Customization: |
Available
|
---|
Basic Info.
Model NO.
|
BH-PAW-150
|
Keywords
|
Orbital Welding Machine
|
Thickness
|
3~30 mm
|
Diameter
|
More Than 150 mm
|
Product Description
Pipe fixed and welding trolley walking are adopted to realize automatic all-position welding. High-efficiency and low-cost CO2 gas shielded welding is adopted for welding process.
BH-PAW-150 Pipeline all-position automatic welding machine is divided into rail type and trackless type. The trackless type adopts magnetic absorption on pipeline,and automatically crawls along the welding path during welding.The installation,use and disassembly can be completed quickly and conveniently. Rail type is mainly used for welding stainless steel or non-magnetic adsorption pipeline, the track specifications according to the welding needs to be customized;
Pipelines all position automatic welding machine is widely used in petroleum, petrochemical, chemical, thermal, gas, Marine engineering, municipal pipelines all position automatic welding in all walks of life, such as using pipe fixed tube, welding carriage to walk the way of all position automatic welding, the welding process with high efficiency and low cost of melting polar gas shielded welding;
All-position welder is mainly characterized by light and portable design, especially suitable for automatic pipe welding on the construction site, with the characteristics of easy to learn, fast welding speed, high production efficiency, good welding mechanical properties, low labor intensity and so on;
Workpieces applicability is wide and more than 150 mm diameter Φ pipes are applicable, without welding thickness limitation in theory, thick tube can use multilayer multiphases welding, welding such as: pipe – weld pipe, pipe, elbow, tee.
Apply to the workpiece | |
Suitable material | Carbon steel, stainless steel, alloy steel, low temperature steel, etc. Non-magnetic material should be equipped with trolley track |
Thickness | 3-30mm |
Diameter | ≥150mm |
Applicable wire | Solid wire or flux-cored wire, welding wire diameter Φ 1.0 1.6 mm |
Applicable position | Full position welding of pipeline, including filling and capping; If argon arc welding is required, it shall be done by manual |
Application weld joint | Pipe – weld pipe, pipe, elbow, tee |
Applicable conditions | All kinds of long distance pipeline welding joints, thermal pipe welding joints buried pipe or process pipe welding joints, whether indoor or outdoor can be safe operation |
Applied environment | |
Location | Indoor and outdoor |
Environment tempera ture | -20ºC–45ºC |
Ambient humidity | 20-90% (no dew) |
Shielding gas | CO2 or 80% Ar+20%CO2 mixture |
The welding quality | |
Appearance of weld molding, no porosity, slag inclusion, incomplete fusion and other phenomena | |
To meet the requirements of pressure test, impact test, tensile test, bending test and other mechanicalproperties | |
Welding process | |
CO2 or Ar and CO2 mixed gas shielded welding, solid wire or flux cored wire welding |
The full-position automatic welding machine trolley can realize constant speed walking along the outside diameter of the pipe, up and down step adjustment of the height of the welding gun, fine tuning of the welding gun, left and right swing of the welding gun, left and right welding stay of the welding gun, welding current and voltage control.
1, Full position automatic pipeline welder adopts advanced design concept and motion control technology;
2, Control mode: microelectronic PCB board + high-definition LCD screen + intelligent waterproof soft button control;
3, Crawling drive: constant torque motor + high precision planetary reducer + worm gear and worm drive;
4, Swing drive: stepper motor + high precision planetary reducer + high precision linear slider;
5, Height adjustment of welding torch: stepper motor + high precision planetary reducer + high precision linear slide rail;
6, Trolley structure: frame structure, made of aviation aluminum alloy;
7, Control features: high-definition LCD screen input parameters, realization of pipe 360 ° 12 welding range, accurate setting each interval of welding technology, digital integrated circuit with CPLD microelectronics and the FPGA chip as the core, the implementation of various motor movement parameters and precise matching of welding current, welding voltage, etc;
8, Welding power supply: imported from Sweden issa digital gas welding power supply, to achieve the welding material in the welding pool of accurate transition control;
1, The main body of the crawler trolley is made of aviation aluminum alloy, with an overall weight of about 14KG, which is convenient to carry in site construction, light in structure and high in strength;
2, The main design size of the crawler trolley is compact, and the rotating space within 300mm around the pipeline can meet the requirement of rotary welding;
3, The walking motor, the oscillating motor and the raising motor of the crawler are all equipped with an orthogonal encoder to achieve position feedback and speed feedback, ensuring accurate position positioning accuracy and speed accuracy, as well as better dynamic performance and output torque;
4, welding gun swing and position adjustment using stepper motor, stepper motor can achieve accurate positioning characteristics, to ensure the width of swing, residence time and high and low attitude control accuracy;
5, The welding power supply adopts digital gas shielded welding power supply, and all welding parameters adopt digital processing, so there is no need for manual intervention in the welding process.
1, The LCD screen + intelligent waterproof soft button control, used for welding program preset, display and parameter fine-tuning, hand-held control box with waterproof design to avoid sweat into the function failure;
2, We developed a new generation of all-position automatic welding machine, crawling trolley walking using our company’s special development of constant torque motor drive, whether downward welding or upward welding, can maintain the speed of crawling welding constant, greatly improve the quality of welding stability;
3, The fourth generation wire feeding machine, wire feeding rolls, special welding torch directly integrated installation on the trolly, such as more compact structure, adopts the design of the cable without welding torch, welding torch, wire feeding machine, all in a car, does not exist when welding torch wire bending problems, greatly improve the welding electric arc stability, at the same time by reducing the wire feeding machine parts made of independent equipment overall quality lighter;
4, Using CPLD microelectronic digital integrated circuit and FPGA chip as the core controller, to achieve the control of the motor, I/O interface control and all the operations. FPGA chip’s high speed operation and timely sequence logic function performance ensure that each motion control and related operation can be completed in a very short time;
5, With X axis straight pendulum and two axis composite pendulum function, regardless of wall thickness, wall thickness, groove girth weld or fillet weld can achieve excellent welding quality;
6, High clarity LCD screen page in the face of “welding parameters setting page” and “monitoring page” to distinguish, to facilitate the setting of process parameters before welding, welding finished switching to the “monitoring page” for real-time observation of welding parameters dynamic, at the same time effectively avoid the welding process in the wrong operation.
A. Mobile welder storage box
It is used to store all components and tools such as welding power supply and trolley, which is convenient for on-site management and transfer between projects. Car body base is equipped with universal wheel, which is convenient for on-site movement and storage.
B. Pipeline automatic welding trolley
Trackless type adopts magnetic absorption on the pipeline, and automatically crawls along the welding path during welding. The installation, use and disassembly can be completed quickly and conveniently. Rail type is mainly used for welding stainless steel or non-magnetic adsorption pipeline, the track specifications according to the welding needs to be customized.
Diameter of pipe | ≥Φ150mm |
Structural style | Magnetic trackless or trackless (material for welding that cannot be magnetically adsorbed) |
Trolley drive | Constant torque motor + worm gear and worm drive |
Trolley walking speed regulation mode | LCD screen setting + soft button adjustment |
Move speed | 290mm/min |
Welding speed | 50-290mm/min;Stepless speed regulation |
Swing drive | Stepper motor + planetary reducer + linear slide rail |
Swing trajectory | Set according to welding requirement |
Swing adjustment mode | LCD screen setting + soft button adjustment |
Swing left and right to adjust the stroke | 78mm |
Swing range | 0.5mm |
Max swing | 30mm |
Swing frequency | 20~60 times/min |
Duration of stay (left, right) | 0~3 seconds |
Swing fine-tuning offset equivalent | 0.1~0.5mm adjustable |
Welding gun up and down adjustment stroke | 128mm |
Up and down electric adjustment | 58mm |
Up and down manual adjustment | 70m |
Weight of trolley | 26KG |
Power of trolley | 120W |
Drive power source | AC 24V |
C. Welding Power Supply
This product is a good performance, powerful function, rich interface, easy to operate digital dc gas welding machine, it has high reliability, easy to upgrade.
Digital welding machine is issa company for the global metal processing and manufacturing to launch a full digital inverter used for automatic welding system for melting polar multi-function industrial welding machine, its excellent arc characteristics, reliability and high efficiency bring higher quality for the customer more efficient welding experience and value, help customers to overtake rivals in metal welding and machining products, to ensure that customers focus on the welding outside the core business, allowing customers to stand out. Adopting dual high-speed CPU and CPLD and its advanced digital control loop, combined with the unique waveform control technology of issa company, the optimization of arc characteristics is realized to ensure the effective control of arc, droplet and pool in the welding process and realize high-quality welding.
Technical features:
1, Leading IGBT inverter technology: the main circuit of this product adopts the international leading high frequency IGBT full bridge inverter technology, significantly reducing the welding machine volume, high power conversion rate; High inverter frequency in addition to audio frequency, almost eliminate noise pollution, so that the welding current is easy to control, welding process smooth and stable.
2, New digital control mode: the control circuit is dominated by a high-performance processor, which realizes the process control of welding, so that the whole welding process from arc ignition, welding, arc closing is smooth transition, arc starting success rate is high, arc closing and cutting ball is fast; Welding machine can adapt to different materials, thickness and shielding gas wire, fine control makes the welding process stable, small splash, wire utilization rate, weld metal fusion good, beautiful shape.
3, Powerful functions: the digital control of high-performance processor enables the welding machine to have many functions that are not available in the traditional analog welding machine, and these functions are particularly important in modern automatic and semi-automatic welding applications.
4, Four types of air protection operation modes: in addition to the two-step and four-step common operation modes, spot welding and repeated (four-step) two practical operation modes are also added.
5, Simple operation: the simple human-machine interaction interface enables the operator to be clear at a glance. The welding mode, welding wire type, gas, wire diameter, etc. can be easily set through the welding machine panel keys. The parameter values of various parameters in the welding process can be set through the encoder. Meanwhile, the welding machine panel and wire feeder panel can set the welding current and voltage (or arc length).
6, High reliability: the product from external structure to internal components are carefully designed and fully tested. For example: the machine from the structure can resist vibration, dust and even metal dust internal electrical components, circuit boards and other special protective process, can make the welder work in a humid environment for a long time. At the same time, the machine has the functions of overheating protection, over-current protection, under-voltage protection, water shortage protection of waterway system, communication fault alarm, etc.
Technical Parameter
Model | MIG500i | MIG350i | |
Input | Input power | 3 phase AC380V±20% 50/60Hz | |
Rated input capacity(KVA) | 24.2 | 13.67 | |
Power factor | 0.92 | 0.89 | |
Output | MMA rated VRD voltage(V) | 15 | 71 |
MMA max rated output(A/V) | 500A/40V | 350A/34V | |
Rated no-load voltage(V) | 80 | 71 | |
Rated maximum output(A/V) | 500A/39V | 350A/31.5V | |
Welding voltage range(V) | 15.5-50 | 10-40 | |
Welding current range(A) | 30-500 | 30-350 | |
Wire feeding speed(m/min) | 1.5-22 | 2.0-22.0 | |
Gas meter heater voltage(V) | AC36V(120W) | ||
Output characteristics | MMA: CCMIG/MAG:CV | ||
Environment | Operating temperature range(ºC) | -10~+40 | |
Storage temperature range(ºC) | -25~+55 | ||
Level of protection | IP23 | ||
Type of cooling | Air cooling | ||
Rated load duration(%) | 50% | 60% | |
Efficiency(%) | 91% | 90% | |
Insulation grade | F | F | |
Size(mm) | 785×330×666 | 630x300x540 | |
Total weight (kg) | 59 | 43 |


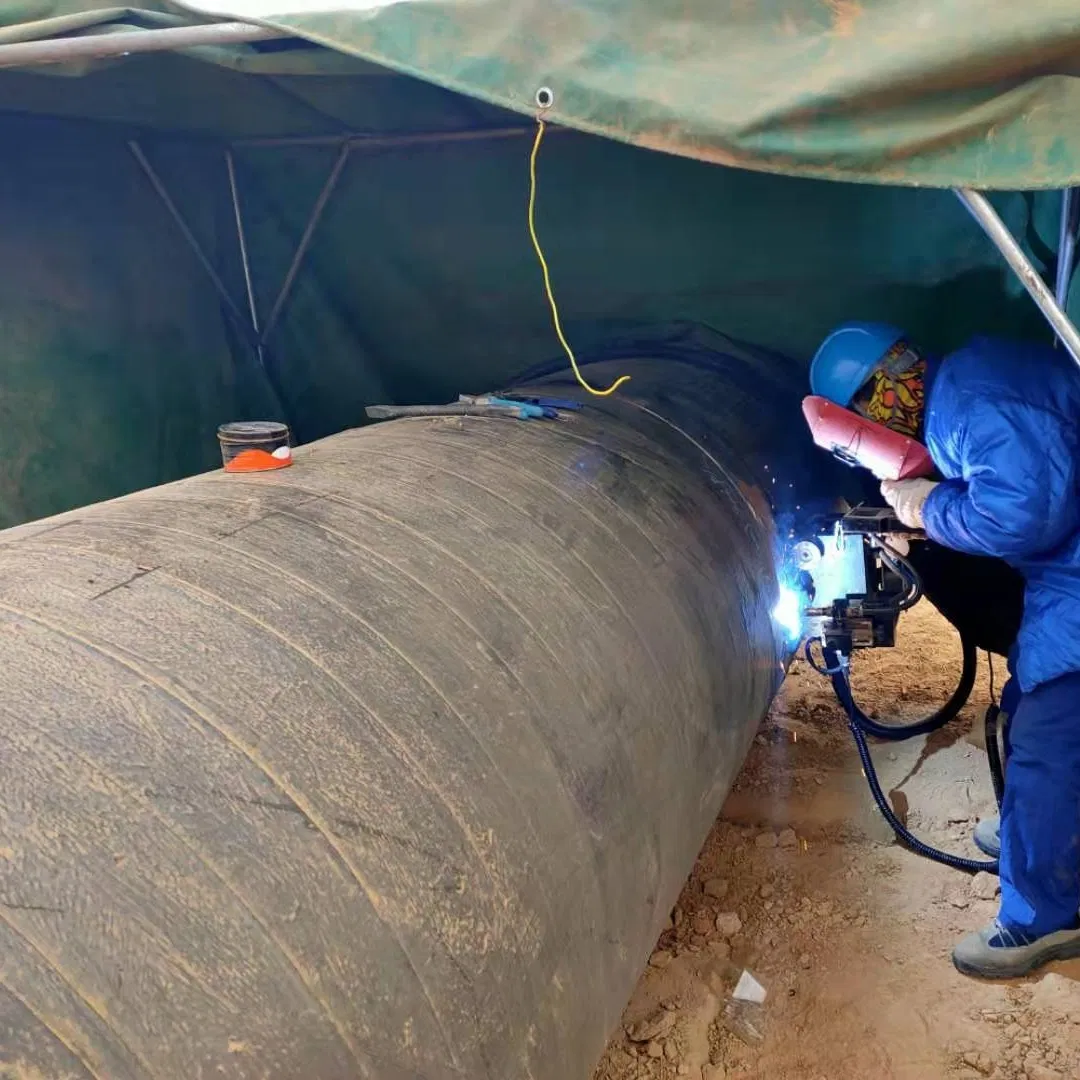
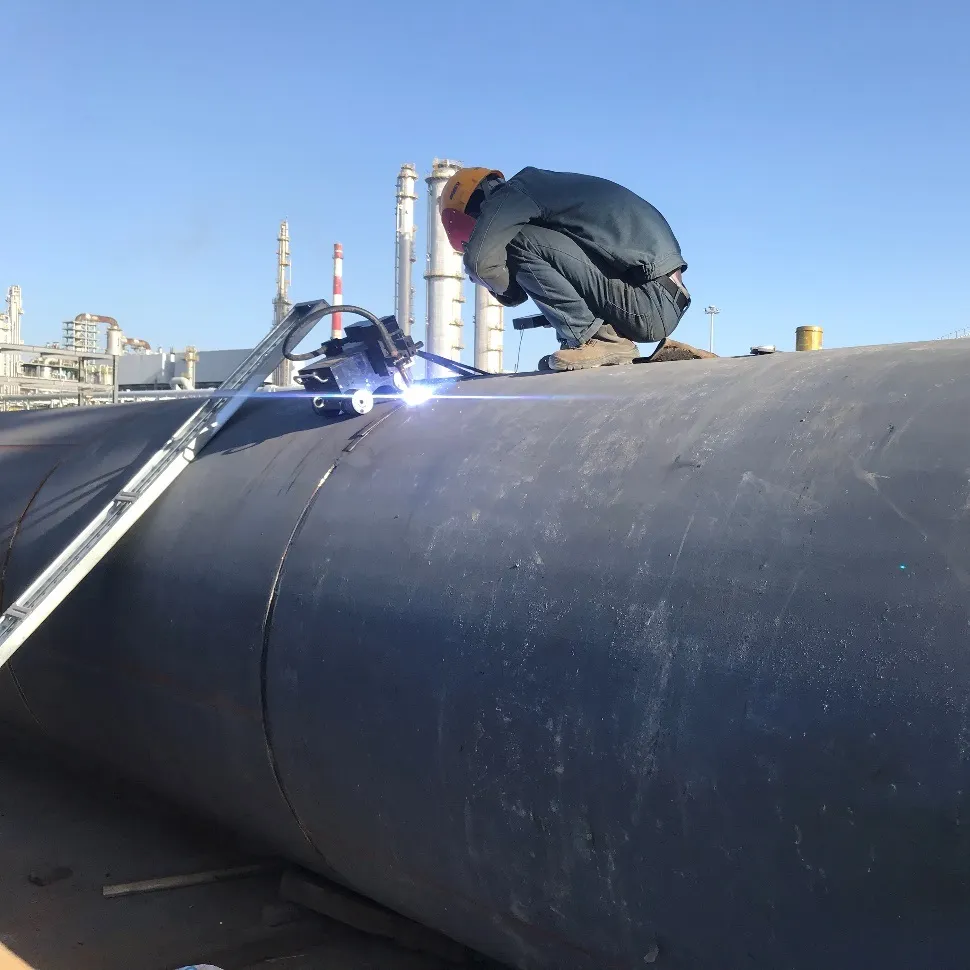
Reviews
There are no reviews yet.